In a step forward for soft robotics and biomedical devices, Rice University engineers have uncovered a powerful new way to boost the strength and durability of silicone-based soft devices without changing the materials themselves. Their study, published in a special issue of Science Advances focused on printed and musculoskeletal robotics, offers a predictive framework that connects silicone curing conditions with adhesion strength, enabling dramatic improvements in performance for both molded and 3D-printed elastomer components.
“We found that the extent to which a silicone elastomer is cured at the time of bonding directly impacts how well it adheres,” said Daniel J. Preston, corresponding author of the paper and assistant professor of mechanical engineering. “By understanding and controlling this variable, we can significantly enhance device reliability without introducing new chemicals or treatments.”
Silicone’s sticky situation
Silicone elastomers are prized across industries — from surgical implants to kitchen tools to soft robots — thanks to their flexibility, chemical stability and biocompatibility. But bonding silicone components together during manufacturing has long posed a challenge. Poor adhesion can lead to delamination, leaks or catastrophic device failure, especially in soft robots where flexible chambers must withstand repeated inflation and deformation.
“Strong, consistent bonding is absolutely crucial in these applications,” said Te Faye Yap, first author of the paper, who received her doctorate at Rice and is now an assistant professor of mechanical engineering at the University of Hawaii. “Consistently achieving this level of strong bonding, however, has been difficult, especially as devices become more complex and rely on multilayered or hybrid designs.”
The issue stems from how silicone cures: During processing, liquid prepolymers gradually transform into solids through a sol-gel reaction. If bonding occurs too late (after the material is fully cured), the interface lacks the chemical cohesion needed for a strong joint. Until now, predicting when that transition occurs under real-world conditions has been difficult.
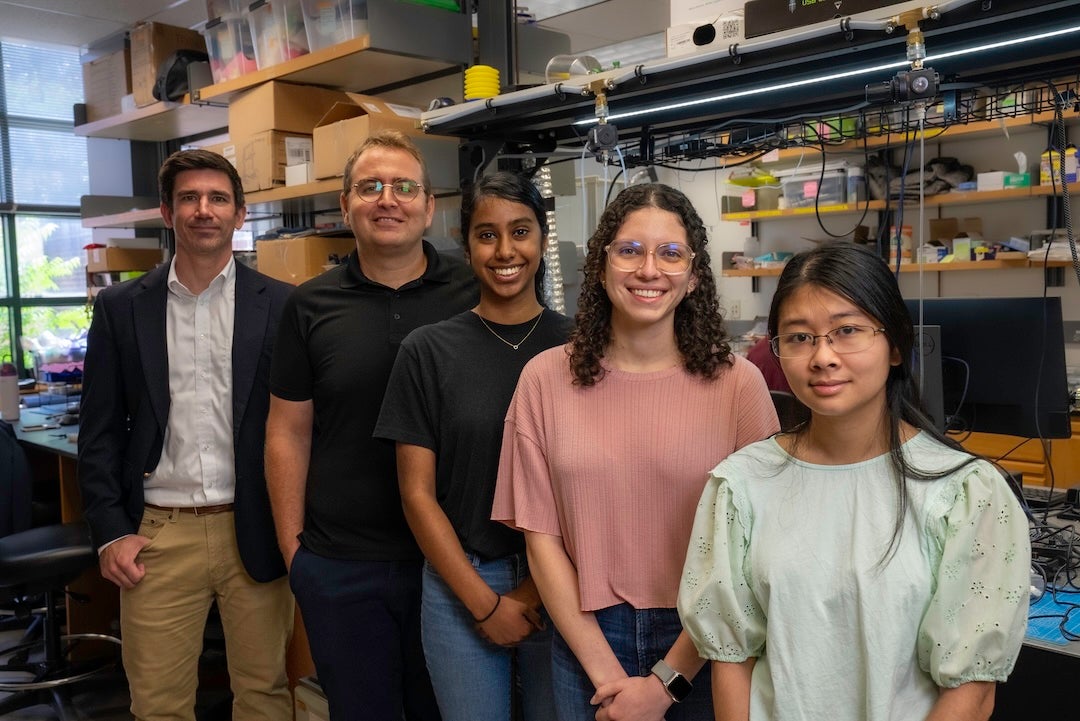
A predictive ‘clock’
To tackle this, the Rice engineering team developed a novel framework that ties the curing process to a “reaction coordinate” — a dimensionless value that accounts for both time and temperature during curing. This metric allowed the researchers to precisely track the degree of curing, even under variable thermal conditions like those found in industrial ovens or 3D printers.
“Our reaction coordinate gives us a kind of clock,” Preston said. “It tells us when the material has partially cured enough to be handled but is still fresh enough to form strong chemical bonds with an adhesive layer.”
This discovery not only clarifies when adhesion is most effective but also helps predict when it will fail. Using peel tests, the team showed that adhesion strength plummets once the reaction coordinate crosses a critical threshold. At that point, newly applied silicone no longer forms robust covalent bonds with the underlying layer, and the interface fails under stress.
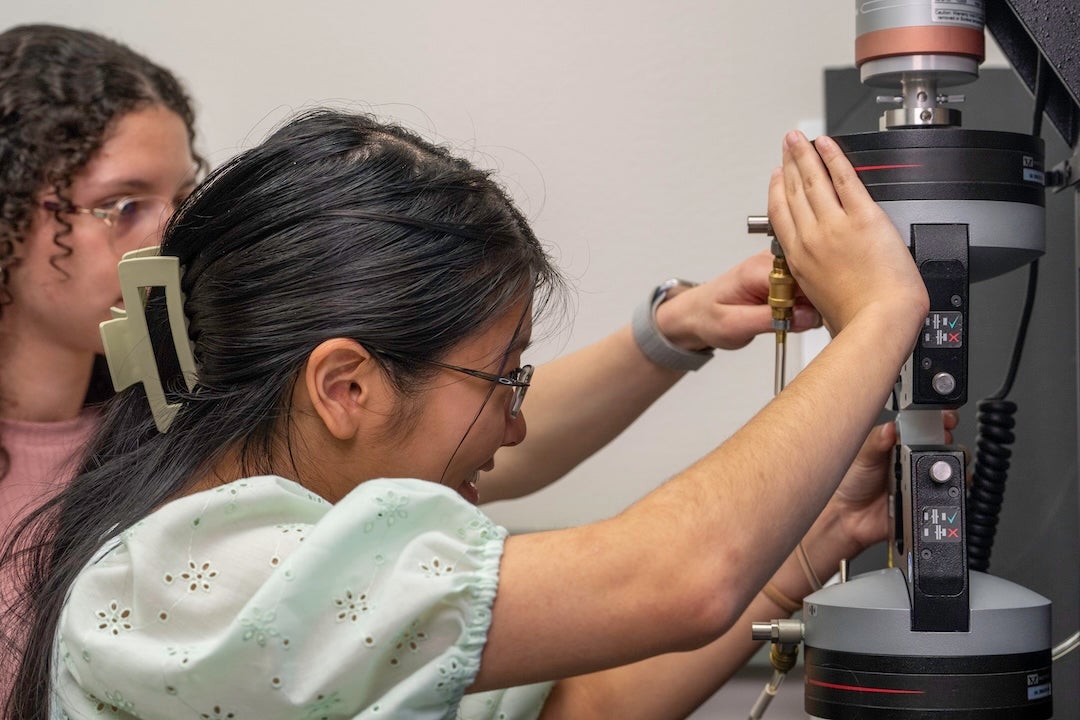
Real-world validation
To prove their model in practice, the team fabricated soft pneumatic actuators (common components in soft robots) by joining precured silicone components using fresh silicone as an adhesive. Devices bonded within the optimal reaction window withstood higher pressures and bent with 50% greater curvature than their overcured counterparts.
In another experiment, the team used a 3D bioprinter to fabricate silicone structures layer by layer. Guided by their reaction coordinate, they precisely controlled the time between printing each layer and achieved more than 200% improvement in interlayer adhesion compared to traditional printing methods.
“We were able to tune the curing conditions to dial in adhesion exactly where we wanted it,” Preston said. “This capability opens the door to stronger, more reliable 3D-printed silicone devices with intricate geometries.”
The implications of this work are broad. Manufacturers of medical implants, wearable electronics and flexible robots could fabricate more durable devices without relying on chemical surface treatments or costly plasma bonding techniques. Additive manufacturing of soft devices, which is an area gaining traction in the medical and wearable tech industries, can particularly benefit from this approach.
“Our framework is simple, generalizable and doesn’t require any new materials,” Preston said. “It’s a guide that engineers can begin using immediately to make better products.”
This research was supported by the National Science Foundation under grants CMMI-2144809, CMMI-2333987 and DGE-1842494 and by NASA through a NASA Space Technology Graduate Research Opportunity Fellowship.
-
Access photos and figures for download.
-
https://rice.box.com/s/4f0nbuc5ub22irq0eg1tam3quhifydo1