
Rice University researchers have revealed novel sequence-structure-property relationships for customizing engineered living materials (ELMs), enabling more precise control over their structure and how they respond to deformation forces like stretching or compression.
The study, published in a special issue of ACS Synthetic Biology, focuses on altering protein matrices, which are the networks of proteins that provide structure to ELMs. By introducing small genetic changes, the team discovered they could make a substantial difference in how these materials behaved. These findings could open doors for advancements in tissue engineering, drug delivery and even 3D printing of living devices.
“We are engineering cells to create customizable materials with unique properties,” said Caroline Ajo-Franklin, professor of biosciences and the study’s corresponding author. “While synthetic biology has given us tools to tweak these properties, the connection between genetic sequence, material structure and behavior has been largely unexplored until now.”
Using synthetic biology techniques, the team worked with a bacterium called Caulobacter crescentus. Previous members of the lab engineered the bacteria to produce a protein called BUD (short for “bottom-up de novo”), which helps cells stick together and form a supportive matrix. This allowed the bacteria to grow into centimeter-sized structures, which the group calls BUD-ELMs.
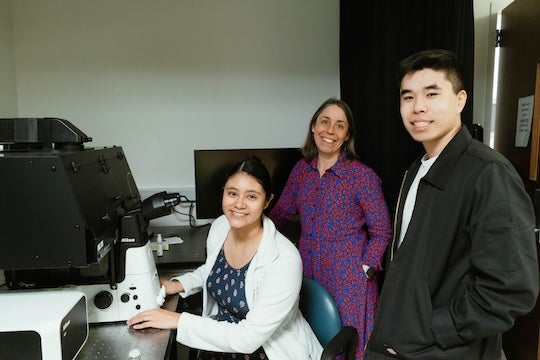
Adopting this engineering approach, the researchers varied the length of specific protein segments called elastin-like polypeptides (ELPs) and created new materials. The team characterized the original midlength BUD-ELM and two new variants and discovered each exhibited different properties. The first material, termed BUD40, had the shortest ELPs and formed thicker fibers that resulted in a stiffer bulk material. The second type, BUD60, had midlength ELPs and created a combination of globules and fibers, producing the strongest material under deformation oscillation stress. Lastly, BUD80, which had the longest ELPs, generated thinner fibers, resulting in a less stiff material that breaks easily under deformation stress.
Advanced imaging and mechanical tests showed that these differences weren’t just cosmetic — they also affected how the materials handled stress and flowed under pressure. BUD60, for example, could withstand more force and adapt better to changes in its environment, making it ideal for applications like 3D printing or drug delivery.
All three materials had two things in common: They exhibited shear-thinning behavior and held a lot of water — about 93% of their weight — which makes them well suited for biomedical uses such as scaffolds to support cell growth in tissue engineering or systems for delivering medications in a controlled way.
“This study is one of the first to focus on building living materials from the ground up with tailored mechanical properties rather than just adding biological functions,” said Esther Jimenez, a graduate student in biosciences and first author of the study. “By making small tweaks to protein sequences, we’ve gained valuable insights into how to design materials with specific mechanical properties.”
The potential uses extend beyond the biomedical field; these self-assembling materials could be adapted for environmental cleanup or renewable energy applications like building biodegradable structures or harnessing natural processes to generate energy.
“This work emphasizes the importance of understanding sequence-structure-property relationships,” said senior Carlson Nguyen, a biosciences major and second author of the study. “By identifying how specific genetic modifications affect material properties, we’re building a foundation for designing next-generation living materials.”
This research was supported by a National Science Foundation Graduate Research Fellowship, the Cancer Prevention and Research Institute of Texas and the Welch Foundation.