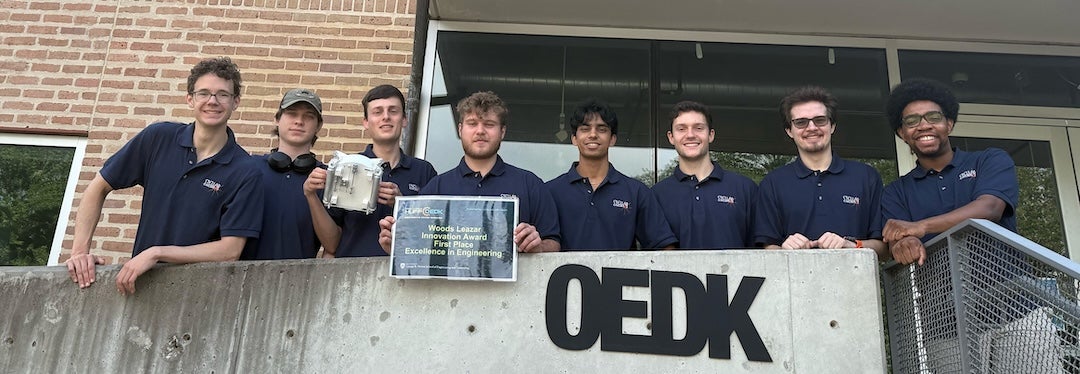
By the end of the decade, the global small satellite industry is projected to nearly double. Small satellites are critical for faster, better and more secure communications and internet solutions as well as environmental sensing, weather monitoring and national security.
A team of Rice University engineering students has designed and built a safer, low-cost propulsion module for small satellites ⎯ a breakthrough that won them the top prize at the 2025 Huff OEDK Showcase and competition, the signature event of the Oshman Engineering Design Kitchen.
The project prompt came from Stellar Exploration, a California-based aerospace technology company looking for a student team that would “really dig into the R&D and document their work,” said Chance Bisquera, a design engineer at the company who mentored the team.
“This is an all-encompassing project that covers a lot of the aspects of what we were looking for in a new system, both from a design perspective and an R&D perspective,” Bisquera said. “Throughout the year, I’ve seen the attention to detail they put in with everything ⎯ that was definitely something that our company had asked for throughout the process, and I think the team definitely delivered and more.”
Warren Rose, StefanBudimlic, Anish Chitnis, Mark Lopatofsky, Jack Maurry, Sam Sarver, Daniel Stulski and Liam Waite signed up for the challenge. As team Thrust But Verify, they spent the past year developing a complete thruster system from the ground up.
The team designed, fabricated and tested a warm gas propulsion system for small satellites featuring a custom cylindrical pressure vessel, optimized supersonic nozzles and a compact thruster array small enough to fit within four CubeSat units.
Their design uses “warm gas” technology to propel small satellites in orbit without relying on conventional hypergolic propellants typically used in spaceflight.
“This is something that is just starting to make its way into the industry. It’s a type of propulsion system that is still pretty underutilized,” said Rose, a mechanical engineering major who will join SpaceX as a life support systems engineer after graduation.
Conventional propulsion systems are difficult to scale down for small satellites. Cold gas-based systems have low energy density, requiring larger volumes of gas to fuel the satellite for sufficient durations. Meanwhile, combustible propellants have much higher energy efficiencies, but they are toxic and difficult to work with, raising regulatory hurdles for testing such as specialized hazmat crews and isolated testing sites.
The new system uses an off-the-shelf, chemically inert automotive refrigerant stored as a liquid and vaporized with heat to generate thrust.
“What this system can provide a massive discount on is that sunken cost in the testing and development phases,” Rose said, adding that the team opted for the most environmentally friendly propellant. “We can test it right here at the OEDK around other students.”
Stulski, a Rice mechanical engineering senior headed to Washington, D.C., to work as a software engineer at Palantir, emphasized the challenge of the scale of the system the team was tasked to develop.
“Our nozzles are tiny. The throat diameter is 0.2 millimeters, so it requires a different level of precision than most other applications,” Stulski said.
To measure thrust at the scale of their system, the team built a custom vacuum chamber test setup capable of detecting forces smaller than the weight of two pennies. Chitnis explained this served to emulate the conditions under which the thruster would have to operate, outside the Earth’s atmosphere.
“This was a way for us to actually validate our models and make sure the whole design could reach performance targets,” said Chitnis, who has an aerodynamics internship lined up at Lockheed Martin over the summer and plans to pursue graduate studies in aerospace engineering at the Georgia Institute of Technology.
In addition to the technical challenges, the project also entailed handling complex logistics. The team adopted a real-world management system where each student took end-to-end responsibility for a major component, mirroring practices at top aerospace firms.
The students credit their time at Rice and the environment at the OEDK ⎯ a 20,000-square-foot facility supporting more than 1,200 students this year ⎯ with preparing them for the demands of high-impact engineering work.
Waite, an electrical engineering major from Florida who collaborated on the system circuitry work and data gathering and plotting for prototype design and validation, learned about Rice through Questbridge.
“It was quite a big leap to come all the way here, but my family encouraged me, and I have zero regrets,” Waite said. “At Rice, you’re really challenged beyond just solving problems ⎯ you develop critical thinking to approach problems that nobody’s solved before. That’s something that employers and alumni say makes a huge difference, and it’s true.”
Maurry, who plans to work in renewables or aviation startups in the San Francisco Bay Area, praised Rice’s welcoming environment, referencing his time on the rocketry club as illustrative of the opportunities to get involved.
“You don’t need to have any previous experience ⎯ you just kind of hop in and learn,” he said. “That’s just an example of how you’re supported to try new things here.”
Sarver, who worked on packaging the system into a compact satellite-compatible form factor, will be joining Amazon Robotics in Boston after graduation. Sarver said his time at Rice and the capstone project experience helped him grow both in terms of engineering but also teamwork and leadership skills.
“My time at Rice has shaped how I approach problems and collaborate with others,” Sarver said. “This project brought it all together — engineering under real constraints, working across disciplines and learning how to lead and adapt as part of a close-knit team.”
Lopatofsky, who earned dual degrees in mechanical engineering and computational and applied mathematics, will join Intuitive Machines in Houston as a propulsion engineer.
“I’ve loved learning here,” Lopatofsky said. “The classes were engaging, the OEDK was an incredible place to build, and the clubs I worked on made Rice a really fun place to be.”
Budimlic, who will return to Rice next year to complete a professional master’s in mechanical engineering before heading to Chevron as a facilities engineer, echoed the importance of Rice’s close-knit culture.
“I really enjoyed my time here. I think the residential college system is really cool,” he said.
From transforming an idea into flight-ready hardware to collaborating with industry sponsors, Thrust But Verify serves as an example of an education that translates into real-world impact. With their award-winning warm gas propulsion system, Thrust But Verify may have helped open new frontiers for the growing small satellite industry.
David Trevas served as the team’s faculty adviser, and the project was sponsored by Chevron.