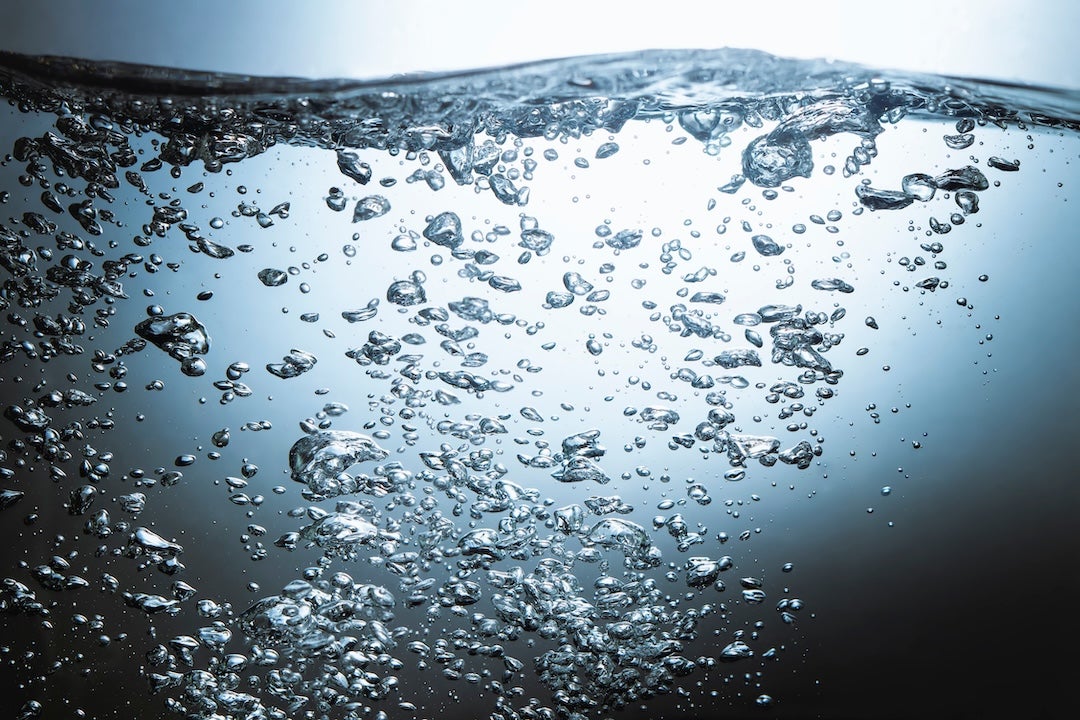
A team of researchers from Rice University, Carnegie Mellon University and other leading global institutions has outlined a bold new roadmap for harnessing heterogeneous catalysis to destroy per- and polyfluoroalkyl substances (PFAS), the so-called “forever chemicals” that have contaminated water supplies worldwide.
In a study published in Nature Water, the international team of environmental engineers, chemists and catalysis experts assessed current catalytic technologies for PFAS destruction, proposed a suite of innovations to overcome existing limitations and emphasized the urgent need for holistic performance metrics that reflect true environmental and public health benefits.
“Catalysis offers a promising path to completely break down PFAS molecules, but current approaches are still far from optimal,” said Michael Wong, co-author and chair of the Department of Chemical and Biomolecular Engineering at Rice. “We need smarter design, better process integration and a more nuanced way of comparing technologies that accounts for energy, cost and toxicity reduction.”
PFAS are synthetic compounds used in products from firefighting foams to cookware and personal care products. Their carbon-fluorine bonds are among the strongest in chemistry, making them extremely persistent in the environment and difficult to degrade. Conventional water treatments such as reverse osmosis and activated carbon filters only separate PFAS from water, meaning toxic waste is left behind.
“Heterogeneous catalysis — the use of solid materials to speed up chemical reactions — has the potential to not only separate but actually mineralize PFAS into harmless by-products,” said Gregory Lowry, corresponding author and a Hamerschlag University Professor of Civil and Environmental Engineering at Carnegie Mellon. “But these systems face multiple hurdles, including poor selectivity, incomplete defluorination and high energy demands.”
One of the team’s key recommendations is a pretreatment step to simplify the complex soup of PFAS often found in industrial waste or contaminated groundwater. Using known homogeneous chemical reactions, they postulate that these mixtures can be transformed into a smaller set of better-understood compounds, paving the way for more effective catalytic destruction.

“Thinking of complex PFAS treatment as a multistep process that will require many steps makes catalyst design much more tractable,” said Sarah Glass, co-first author and graduate student in civil and environmental engineering at Rice. “Designing and using treatment techniques that are really efficient for a certain step of degradation can improve overall efficiency and accelerate the development of real-world catalytic solutions.”
The researchers proposed a sequential “treatment train,” where simplified PFAS mixtures are processed through tailored catalytic steps. First, the process removes specific chemical head groups from the PFAS molecules. Next, it shortens their long perfluorinated carbon chains, stripping away the fluorine atoms — the key to their persistence. Finally, the remaining fluorinated fragments are broken down into safe, naturally occurring substances like carbon dioxide, water and fluoride ions. Each step uses a specialized catalyst tailored to the chemical structure at that stage. For example, titanium-based materials are used to speed up oxidation, while palladium helps swap out fluorine atoms for hydrogen in a process called reductive hydrodefluorination. This approach ensures that even complex PFAS mixtures can be effectively destroyed rather than just absorbed onto a solid, requiring additional treatment.
“Think of it as a relay race,” said Thomas Senftle, co-author and the William Marsh Rice Trustee Associate Professor in Chemical and Biomolecular Engineering at Rice. “Each catalyst hands off a partially degraded PFAS to the next until the molecule is completely broken down. Our goal is total defluorination.”
The researchers stressed the importance of creating catalysts that can target and break down PFAS without being distracted by other substances commonly found in contaminated water. To do this, they are exploring catalyst surfaces that better attract PFAS and are using computer models and machine learning to predict reactions and optimize catalyst design.
“We’re still learning which PFAS break down under which conditions,” said Pedro Alvarez, co-author, the George R. Brown Professor of Civil and Environmental Engineering and director of the Rice Water Technologies Entrepreneurship and Research Institute. “Data-driven simulations can dramatically speed up the discovery process.”

The team also introduced a new energy metric called electrical energy per order of defluorination (EEOD) to fairly compare how efficiently different catalytic systems break fluorine-carbon bonds. Unlike traditional removal metrics, EEOD focuses on true degradation, not just separation.
The study concludes with a call for interdisciplinary collaboration and open data sharing to refine PFAS treatment strategies, with the need for scalable, cost-effective destruction methods greater than ever.
“PFAS are a generational challenge,” Wong said. “We owe it to future generations to find smart, sustainable solutions, and catalysis can be one of them.”
This research was supported by funding from the National Science Foundation, the National Institute of Environmental Health Sciences, a Dean’s Fellowship from the College of Engineering at Carnegie Mellon and the National Natural Science Foundation of China.