Public transit operators keep cities moving, helping people get to work, attend medical appointments and access essential services. But while passenger safety is often in the spotlight, the health and well-being of drivers who spend long hours behind the wheel is frequently overlooked.
That’s the issue a group of senior engineering students at Rice University set out to address.
Known as the Cushion Queens, the team of Belen Szentes, Emily Peña, Eva Montenegro, Gretchen Schulke and Leticia Souto designed a low-cost, air-powered mechanotherapeutic seat for bus drivers. Their goal? Relieve chronic back pain and muscle fatigue from prolonged sitting using an innovative textile-based solution that doesn’t rely on electronics.
“We specifically designed it for the Rice bus shuttles,” Peña said. “They already have compressed air systems built in, so we were able to tap into that existing infrastructure and create something simple, effective and easy to integrate.”
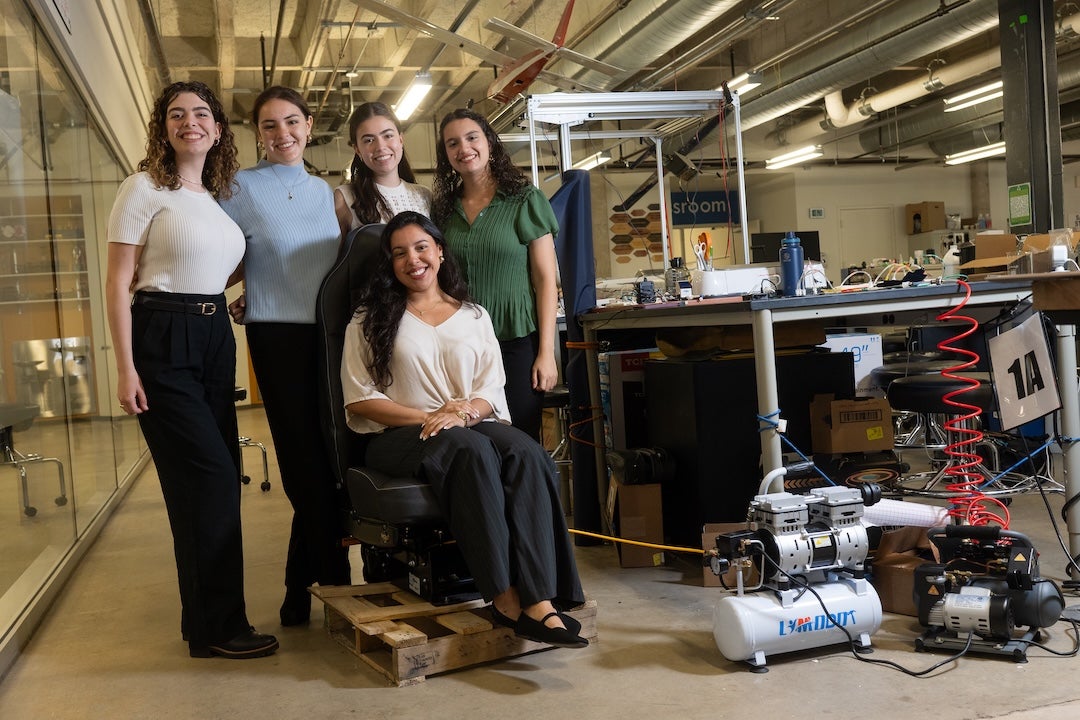
Their design, built as part of a capstone project in the Oshman Engineering Design Kitchen (OEDK), uses fluidic logic — a system of controlling air flow through flexible channels — to provide a rhythmic massaging effect. Rather than relying on expensive electronics or motors, the seat uses air alone to create the massaging motion. The work was supported by faculty adviser David Trevas and funded through the Bob and Lori Herlin Endowment for Design. Notably, the team won the second place Excellence in Capstone Engineering Award as well as the first place Willy Revolution Award for Outstanding Innovation at the Huff OEDK Engineering Design Showcase in April.
At the heart of the device is a series of thermoplastic polyurethane-coated textile pouches, manufactured by heat-sealing layers of material in a specific pattern. The team used a masking technique during fabrication that prevents certain areas from sealing, leaving open-air channels. These channels route compressed air to different parts of the cushion.
“The way it works is that air flows into the first pouch, which inflates and then blocks its own channel,” Schulke said. “That forces the air to reroute to the next pouch in the sequence. As that pouch inflates, the previous one deflates, and it keeps going in a loop. This unstable equilibrium creates a continuous wave-like motion, just like a massage.”
This self-regulating oscillation mimics more complex massage systems but without the need for solenoids or microcontrollers. In fact, the team was able to replace a bulky, standard $60 valve block with a smaller, 60-cent textile pouch, dramatically reducing both cost and complexity.
The system also includes tunable resistors, which help control airflow and timing by providing a controlled air outlet from the pouches. Originally developed in Daniel Preston’s lab, the core concept was modified by the students for real-world use in vehicle seating. They redesigned the flow path so that resistors are now in series with the pouches, rather than in parallel, improving the function and simplifying the build.
“We had to iterate over and over to get the pouch manufacturing right,” Souto said. “Just learning how to cut and seal the heat-sensitive fabric without damages and leaks took us the majority of the first semester.”
Alongside technical problem-solving, the team also learned to navigate the sourcing of niche components, often reaching out directly to international suppliers and negotiating specifications.
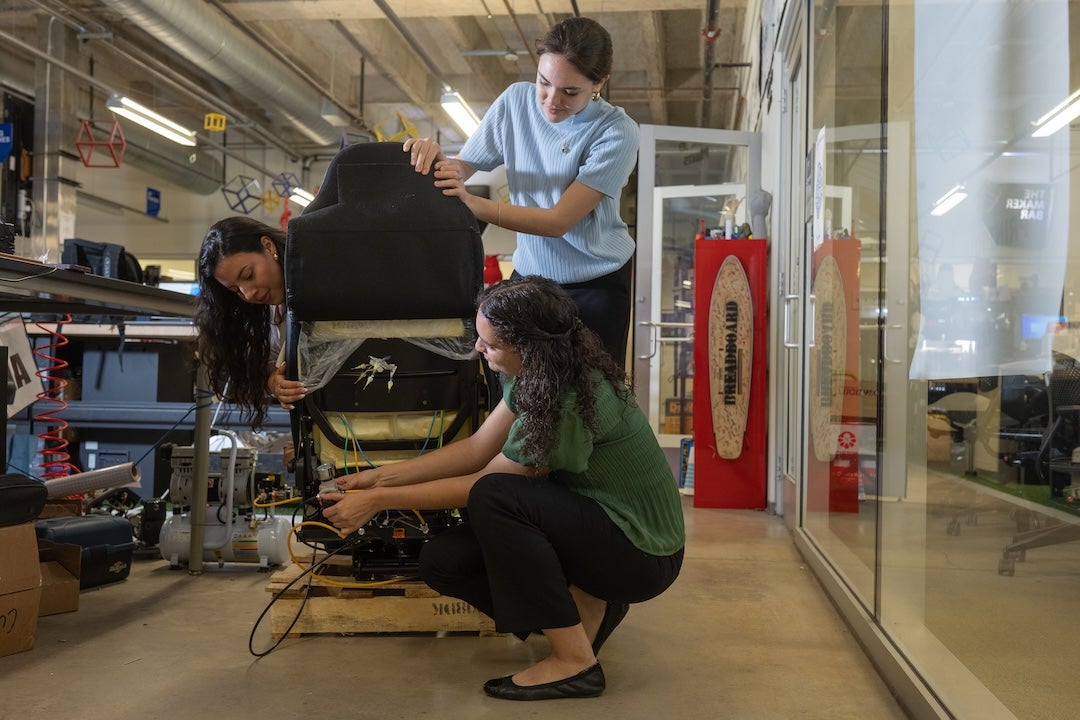
Early feedback from bus drivers has been enthusiastic.
“One driver we interviewed was really excited,” Montenegro said. “He said the current lumbar support just pushes you forward and doesn’t actually help. Our cushion, on the other hand, provides actual movement and relief to the lower back.”
The team is working to gather more data using pressure sensors to demonstrate how the massage rate and forces applied to the body compare to commercial products. This information will be valuable, especially considering that their design could support other innovations across different industries.
“This same concept could be applied to office chairs, hospital beds or wearable medical devices — anywhere there’s a need for gentle, programmable pressure without electricity,” Szentes said.
The students agreed that working on the project gave them invaluable hands-on experience.
“It taught us persistence, because building something real is not like a homework problem,” Schulke said. “It takes time, trial and error and teamwork.”
Video credit: Gustavo Raskosky/Rice University; photos by Jeff Fitlow/Rice University.