After years of development, an elite team of professional bassoonists from across the country including representatives from Rice University gathered at Purdue University Fort Wayne’s Auer Performance Hall to test a new bassoon prototype from Fox Products. It was an exciting moment that Sarah Thelen, Fox’s vice president of product engineering, said she couldn’t miss — even just two days after giving birth.
“She stopped by on her way home from the hospital,” said Fox marketing specialist Stephanie Patterson.
Thelen said she simply had to hear what Fox’s new Model 750 sounded like in the hands of Metropolitan Opera Orchestra principal bassoonist William Short, Rice Shepherd School of Music’s Lynette S. Autrey Professor of Bassoon Benjamin Kamins, Saint Paul Chamber Orchestra principal bassoonist Andrew Brady and Houston Symphony principal bassoonist Rian Craypo. Short and Craypo are Shepherd School alumni, and Brady was accepted into the school’s master’s program before chosing a professional path.

“Because everyone has biases, preconceived notions and, in many cases, blind spots, I didn’t want to be the sole opinion-giver in this process,” said Short, who was Fox’s initial point of contact as it started the development process for the new model. “We all felt that it was important to not have people from the same bubble — pedagogically, musically, educationally.”
Short connected with his former professor Kamins, whom Short called “brilliant,” then he added Craypo (who “speaks the same language” as Short) and Brady (“an exceptional bassoonist and musician”) to the list of instrument testers.
“We are immensely proud of our Shepherd School faculty member Ben Kamins and his star alumni who played such a pivotal role in the development of this new bassoon,” said Shepherd School Dean Matthew Loden. “Their work sits beautifully at the intersection of innovative engineering, artistic craftsmanship and musical knowledge, and further highlights the significant impacts Shepherd School musicians are making to advance the musical arts.”
Brady said he was impressed by Fox’s openness throughout the process, which included seeking out players who didn’t use Fox instruments professionally.

“Fox is smart in that they saw there was a segment of the market they were missing,” Brady said. “The fact that they were curious about finding out what that was and addressing it, it’s amazing.”
“We’ve known for a while that we have been missing a segment of the professional bassoon market,” Patterson said. “We have a lot of models that were quite popular in the ’80s and ’90s, and people still love those, but we were not meeting the needs of a section of the bassoon market that this development team falls into.”
The goal, Patterson said, can be traced back to Hugo Fox, the bassoonist who founded Fox Products 75 years ago. Fox, who played with the Chicago Symphony for nearly 30 years, wanted to develop quality instruments with an affordable price tag. These days, Kamins said professional bassoons from other companies start at $50,000.
“All of us share this really strong belief, both practically and for the sake of our students ethically, that there needs to be more really top quality instrument options that are more accessible, that are more affordable, that will help these students who don’t have the resources still be able to accomplish what they hope to accomplish,” Short said. “That was the real impetus for all of us.”

Because Fox doesn’t sell its instruments directly to consumers, but through dealers all over the country, there’s not a set price for the Model 750. As an example, Shepherd School alum, Houston Symphony principal contrabassoonist and Fox dealer Adam Trussell lists the model at $37,750, though he said he can offer special pricing for those who contact him directly.
Short said the project was also appealing because all of Fox’s products are made at its factory in South Whitley, Indiana, which makes maintenance and customization more accessible.
“Our careers rely on this instrument, so you have to find someone you really trust who can do quality work and, crucially, not damage the instrument,” Short said.
“To have an American company making, servicing and customizing instruments of the highest quality is not a luxury the domestic bassoon community has ever had,” said Kamins. “So in addition to extraordinary instruments, there will now be a network in the U.S. for the long-term support of the instrument. This is huge as we now depend on a very small handful of master artisans to keep our instruments in top working order. Often we have to wait up to six months to make an appointment with them and now will have much more reasonable options.”
With musicians assembled and a common goal in mind, Fox got to work building a new bassoon from the beginning. The process started in early 2020 by reviewing existing instruments, which wasn’t easy during the COVID-19 pandemic. Instead of gathering everyone together, Fox sent five of its existing bassoons to the musicians to assess what the instruments’ best elements were.
“We created a standardized spreadsheet and list of criteria for people to assess each instrument on,” Short said. “We even recorded ourselves playing predetermined pieces on them, just so we could be sure that we were really speaking the same language.”
Fox bassoons, Brady said, have always had a consistent quality, but the team wanted to add complexity, depth and variability of sound.
“After our observations were noted, the Fox team hunkered down to make a new bassoon based on our observations and desires,” Craypo said. “Over the next year or two, they would update us every once in a while with their progress, eventually bringing several prototypes and the entire consulting team down to Houston for trial in various acoustic spaces.”
One of those spaces was the Shepherd School’s Duncan Recital Hall in Alice Pratt Brown Hall. During those meetups, the musicians would take turns playing Fox’s prototypes as well as their own instrument.
“The feedback from this visit helped determine final manufacturing decisions for finish and keywork designs and placement,” Craypo said.
It all culminated with a visit to Indiana this spring, where the musicians visited the Fox factory and got to play the final prototype at Purdue Fort Wayne, an opportunity that Brady said gave him chills.
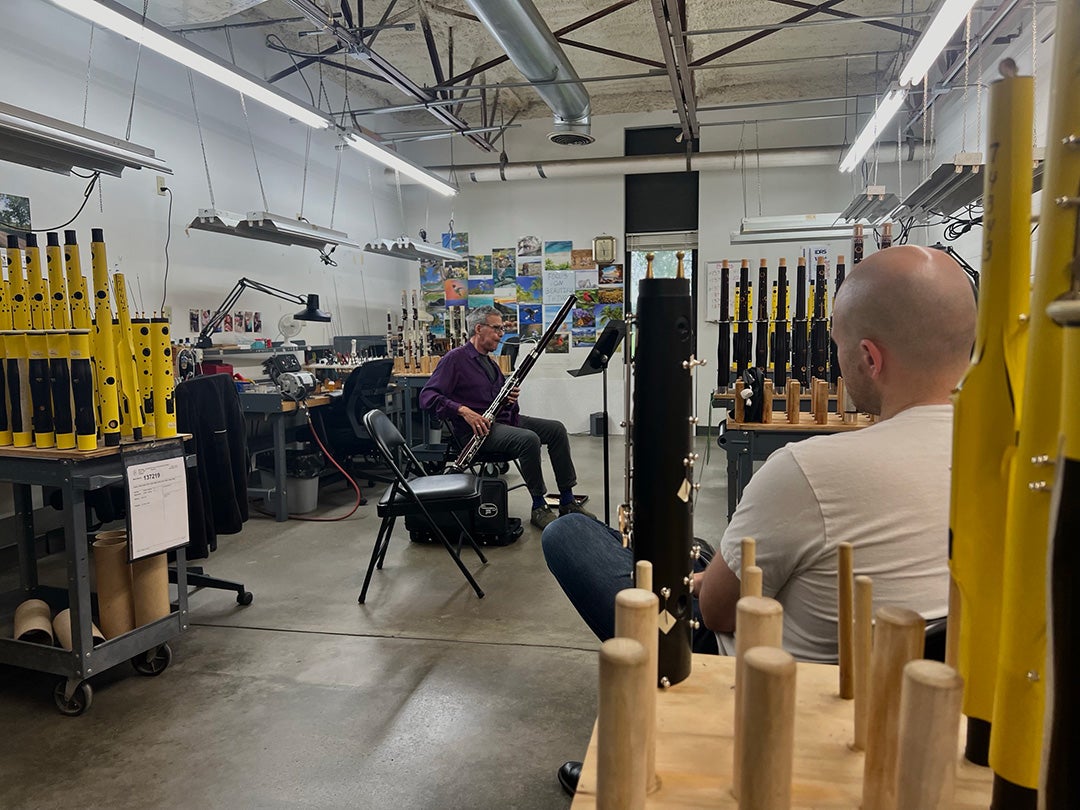
“We went through one round of prototypes, and we went over every square millimeter of this instrument,” Short said, adding that as soon as he played it, he knew it was his favorite Fox bassoon. “We really put it through its paces playing-wise, all four of us separately, all four of us together, in various places and in various configurations.”
“The bassoonists were trying the instruments on the stage, and we were listening in the concert hall,” said Janet Rarick, Kamins’ wife and associate professor of music career development at the Shepherd School. “The engineers were also on stage making immediate adjustments.”
Those engineers all have music degrees as well, said Fox Products president Gabe Starkey.
“We’re grateful for our team at Fox,” Starkey said. “We’ve got about 140 people here who work so diligently and passionately on the instruments. We would not be anywhere without their hard work and dedication. They pour a lot of hard work and skill into these instruments, so we can enjoy the position we have in the market.”
“Everyone involved in this process is a musician, often an accomplished one,” Short said. “It’s really rare in my experience to find people who genuinely want honest, unvarnished feedback.”
The result is a new bassoon that blends Fox’s renowned mechanical stability with the power and flexibility needed by professionals. The team said it delivers a strong core sound at all dynamics, an easy and stable tenor register and rich low tones without pitch compromise. Boasting thicker walls and a robust sound, Fox added that its Model 750 can project over a large orchestra while maintaining a beautiful tone.
“It was fascinating learning about what goes into developing a new instrument and watching a highly organized team build something from scratch,” Craypo said. “I’ve always enjoyed the problem solving and brainstorming side of projects and was honored to have been invited into this project with other colleagues I hold in high esteem. I’m grateful to Fox for seizing this opportunity to expand their offerings and meet a need in our community.”
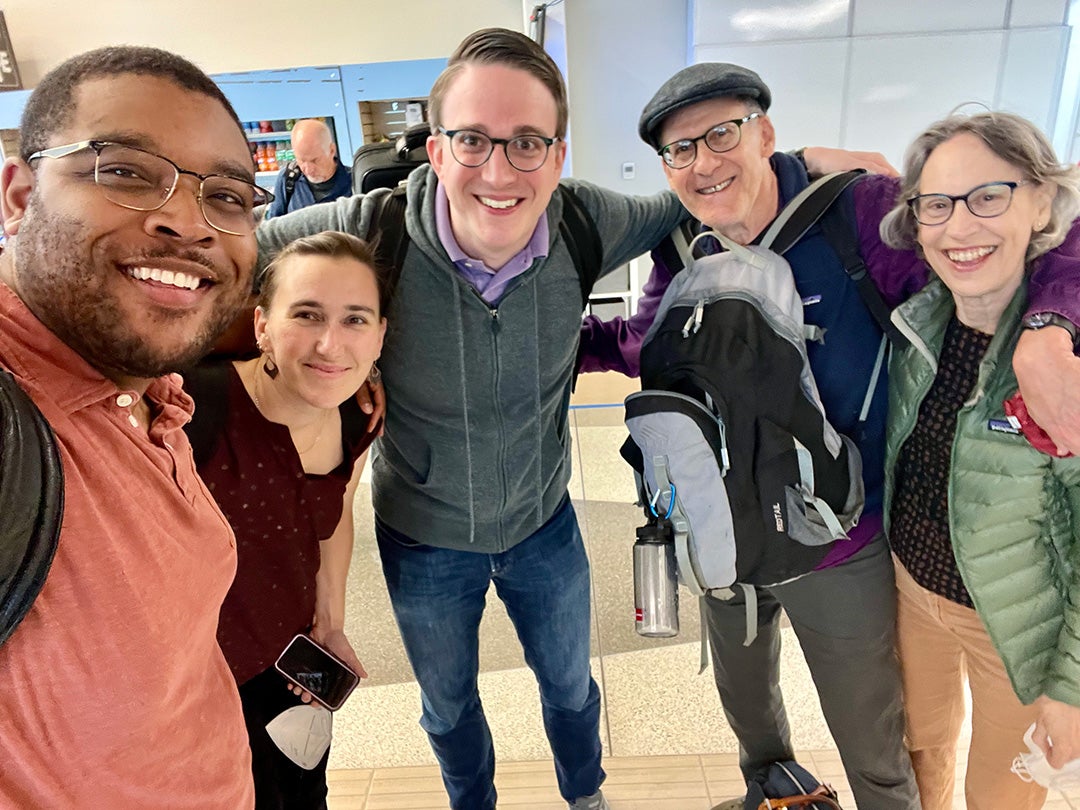